User Guide for the MRO-Tracker 5.0
This document provides detailed information for your company to successfully use the improved MRO-Tracker web application with your MRO customers and suppliers.The purpose of this document is to guide you to fully understand and support the MRO-Tracker EDI process and requirements.
Should you have any questions or concerns, please do not hesitate to contact us at support@b2b-aero.com
Table of Contents
I | INTRODUCTION |
II | MRO-TRACKER FUNCTIONALITIES |
II.1 | REPAIR ORDER SEARCH |
II.1.1 | Search |
II.1.2 | Repair Order Details |
II.1.3 | Settings |
II.2 | ONLINE DATA ENTRY |
II.2.1 | Acknowledgement |
II.2.2 | Quotation |
II.2.3 | Partial Quotes |
II.2.4 | Repair Status |
II.2.5 | On Hold Start/Stop |
II.2.6 | Return Shipment |
II.2.7 | Upload Document |
II.2.8 | Messages |
II.3 | REPORTING |
II.3.1 | Access a Report |
II.3.2 | Filter a Report |
II.3.3 | Create a New Report |
II.3.4 | Run / Save / Download / Edit a Report |
II.3.5 | Schedule a Report |
II.3.6 | Share a Report |
II.3.7 | Report Options |
II.3.8 | Report Context Menu |
III | APPENDIX - SUPPORT CONTACTS |
IV | APPENDIX - EDI IMPLEMENTATION OPTIONS & UPGRADE |
V | APPENDIX - CAPABILITY LISTING |
I Introduction
b2b-aero.com is proud to present the upgraded MRO-Tracker Version 5.0 with many improvements that result from constant development and valuable user feedback.The system employs easy-to-use E-Business and Internet Communication Services. MRO-Tracker capabilities include:
• automated transfer of advanced repair order notifications
• monitoring of the entire repair order cycle progress
• automated exchange of repair order data and related information
• online file upload and document storage ( e.g. SFR – shop finding reports, certificates,…any document)
• creation and customization of repair order status reports
• automated distribution (e-mail delivery) of repair order status reports
• RFQ & Quotes exchange, montoring and management
• AWB and transportation tracking
• supports any data format & transfer process
• can be used with (all) other customers (one-time-setup/implementation)
We encourage you to quickly explore the new MRO-Tracker and its new user interface! Please take the time to familiarize yourself with the b2b-aero.com MRO-Tracker system and please do not hesitate to contact our product experts at support@b2b-aero.com if you have any questions or to schedule a web-training-meeting!
It is our expectation that the new MRO-Tracker will simplify our companies repair order management, monitoring and reporting tasks with your MRO partners and we are positive that it will take inefficiencies, manual intervention and costs out of our business operations!
II MRO-Tracker Functionalities
II.1 Repair Order Search
II.1.1 Search
II.1.2 Repair Order Details
The figure below shows the repair order details including acknowledgement data. Red exclamation marks will indicate stored information. To return to your latest query pulled from the database just click on the Reports tab at the top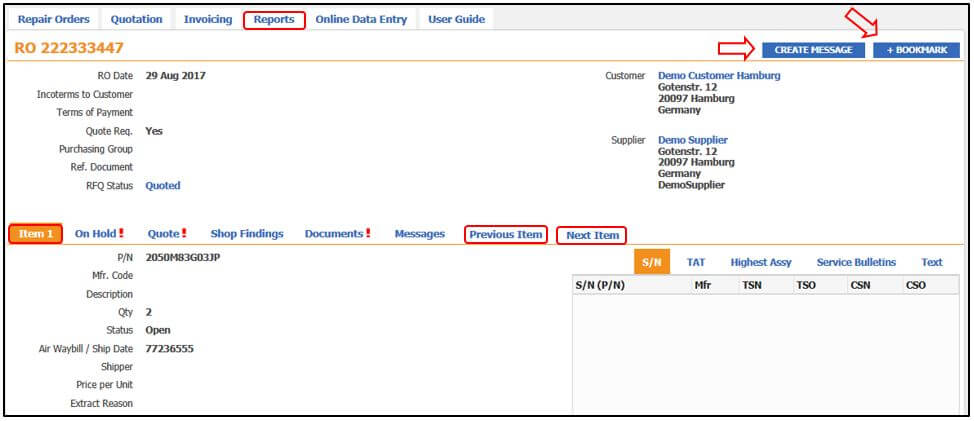
Since the MRO-Tracker is line item based you can switch between different line items of the same repair order by clicking on “PREVIOUS ITEM” or “NEXT ITEM”.
From this repair order overview page you can use “CREATE MESSAGE” to get in contact with the responsible purchasing manager (see Chapter II.2.7 Messages) or “+BOOKMARK” the repair order. Bookmarked repair orders will appear as a shortcut at the bottom of the MRO-Tracker landing page (see Chapter II.1.1 Search ).
The following sections will describe the online data entry functionality and enable you to provide repair order status through your browser at any time.
II.1.3 Settings
MRO-Tracker quick access tab for settings offers users enhanced convenience, allowing them to easily configure whether they want new Purchase Orders (POs) to open in new tabs or not. These same settings can also be found under the "My Settings" section in the user profile, giving users flexibility in how they manage their workflow and navigation preferences.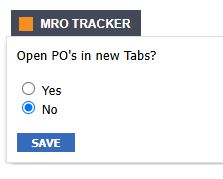
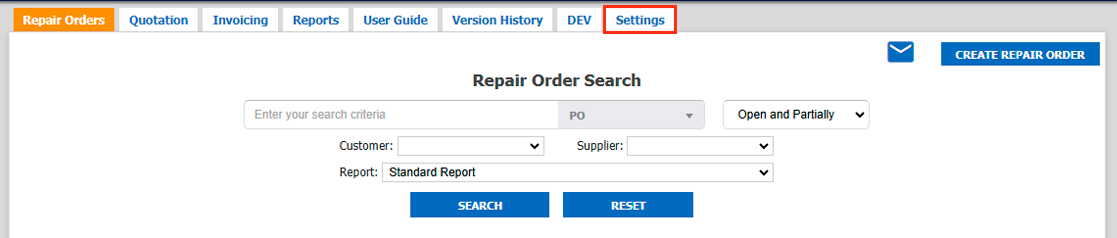
II.2 Online Data Entry
II.2.1 Acknowledgement
Upon receipt of the unserviceable unit from the customer, you will start the order acknowledgement by providing the “goods received” information (supplier in date, qty. received etc.). In order to create an acknowledgement via the online data entry functionality, you will have to select and open the order item and then click on “CREATE ACKNOWLEDGEMENT”.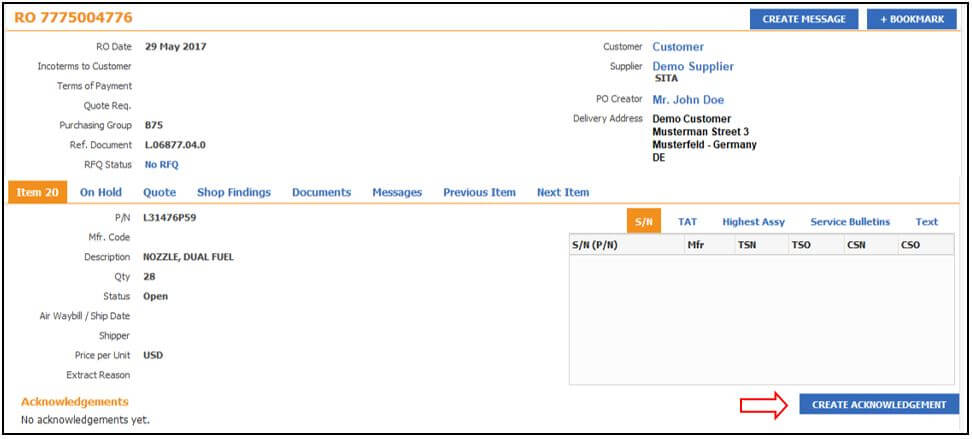
After opening the “Create Acknowledgement“ submenu please enter the following (*mandatory) information and feel free to include additional information (see figure next page). After entering the data confirm by pressing “SAVE”.
Please fill in following information:
• Quantity (received)
• Supplier In Date (goods receipt date)
• Part Number (P/N) (received)
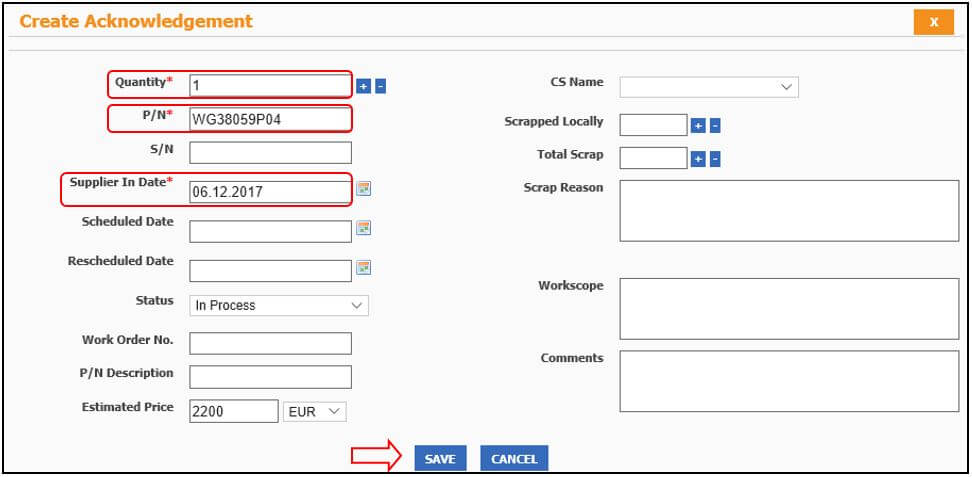
II.2.2 Quotation
MRO customers can “flag” orders that require a Quotation from the repair vendor. You will receive an RFQ by e-mail if a quote is required. Please open the Quotation page to create a quote online. You can query the Quotation database by different repair orders – e.g. “RFQs without quote” or “Repair Orders without a Quote”.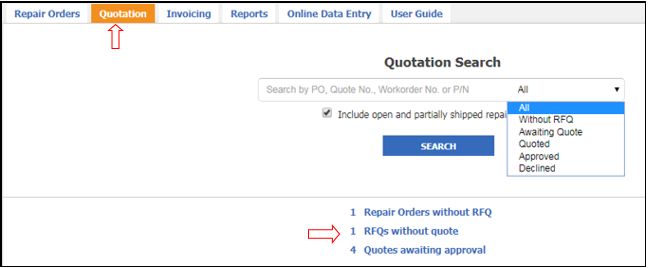
Please click on the repair order number to open the Quotation submenu.

Please provide most critical Quotation information and add further details to support an accurate data exchange.
Mandatory data is:
• Quote Number
• Serviceable Qty
• Total Repair Price (only if Serviceable Qty >= 1)
• Work scope
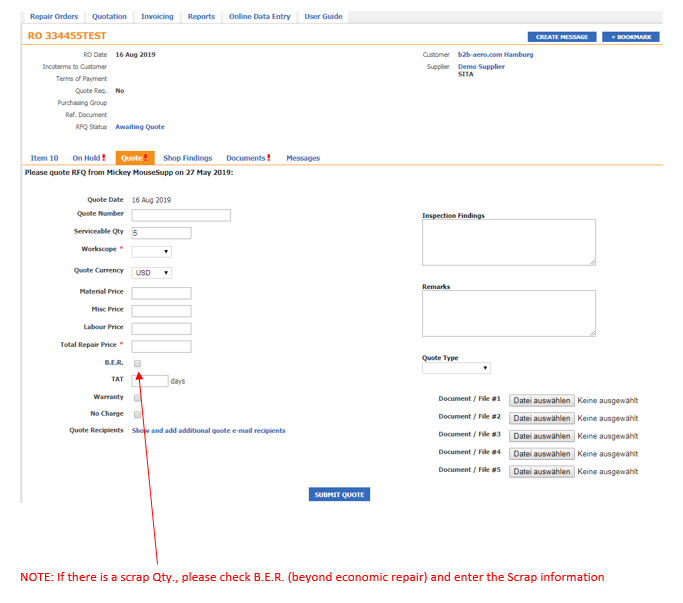
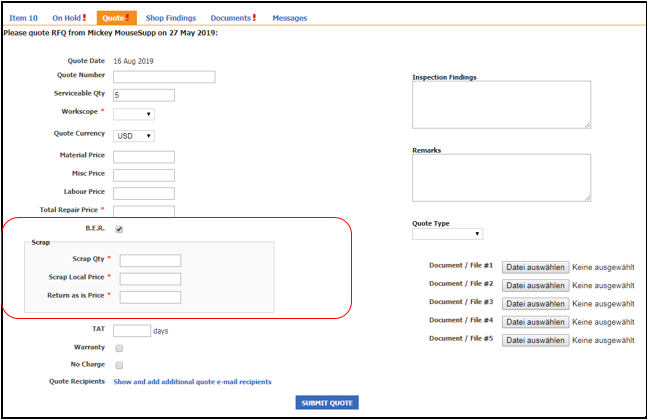
Feel free to attach one or several documents by clicking on the “Browse” buttons.(1) Select your prefered quote file(s) from your computer and continue with “Open” (2) to add these documents to the quotation. Save & transmit the information by clicking “Submit Quote”.
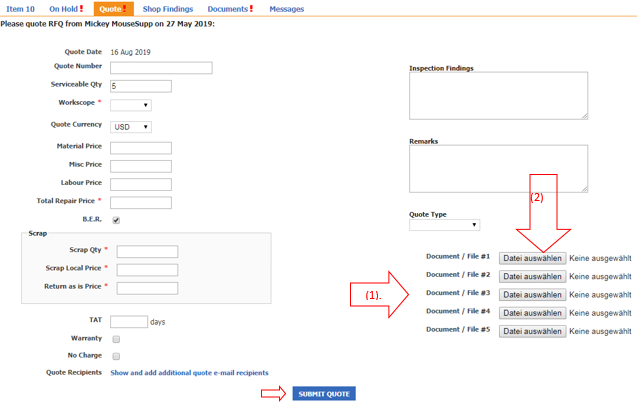
You can requote the repair order at any time until the Quote has been approved by your MRO customer.

MRO customers can approve Quotes online by navigating to the Quote menu
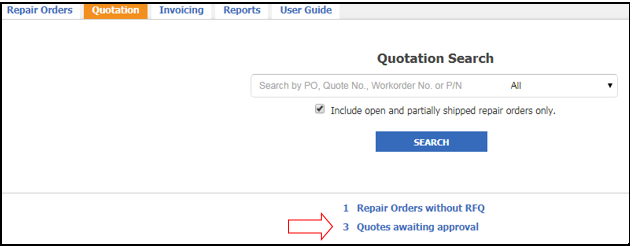
Quotes can also be approved directly “in” a specific Repair Order:

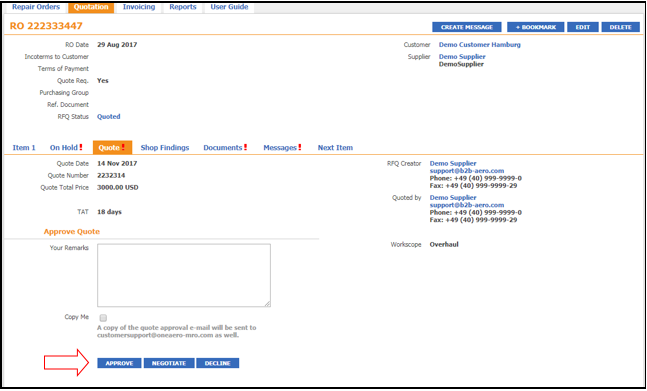
Here you have the following options to answer a quote:
• Your Remarks (enter individual annotations)
• Copy Me (send a copy into your own inbox)
• APPROVE
• NEGOTIATE
• DECLINE
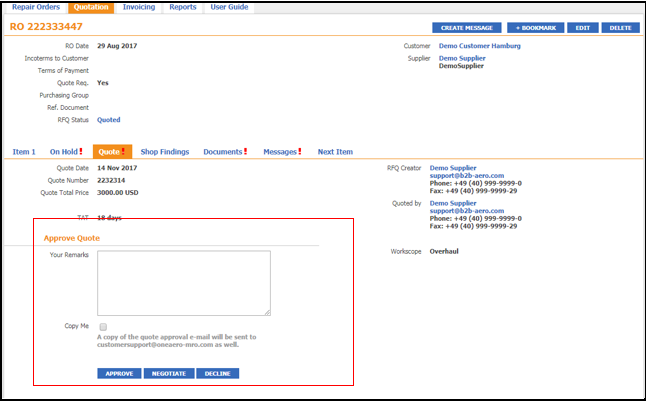
II.2.3 Partial Quotes
The MRO-Tracker Quotation module also allows you to create multiple quotes on a single (specific) repair order line item that shows a quantity > 1To generate the first partial quote in our system please refer to Chapter II.2.2)
Please make sure that you enter the “correct” < Serviceable Qty > ! The qty. should only cover the number of parts you want to quote for !
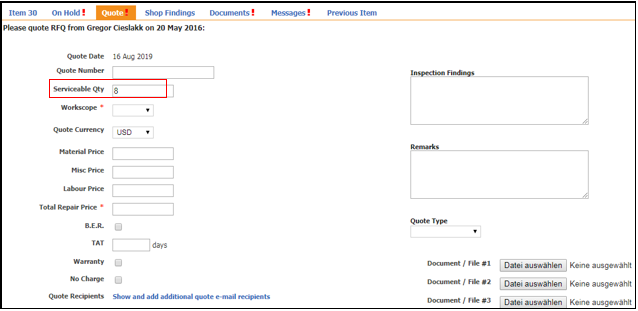
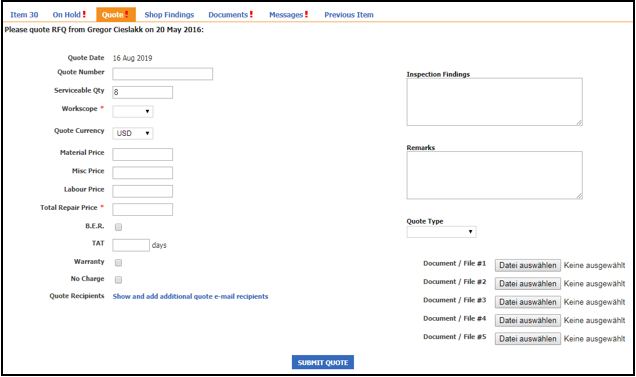
Find your “partial” Quote “history”
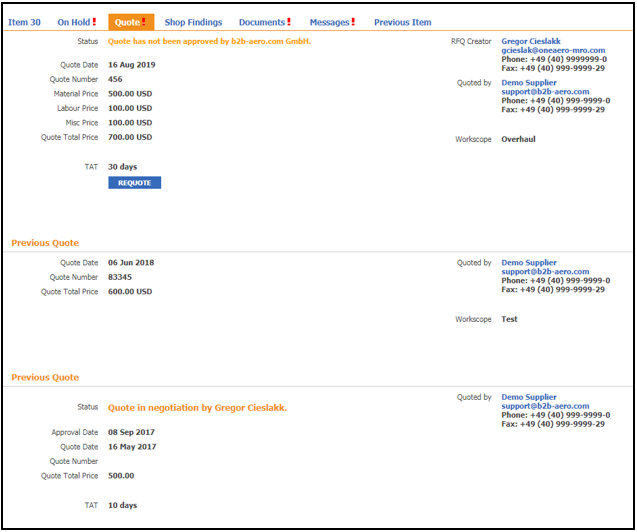
II.2.4 Repair Status
At any time during the repair process you can update/edit your repair order status information. Go to the RO item detail screen (see Chapter II.3.2 Acknowledgement) and enter your data there. Please click on “Edit” to reopen the “Create Acknowledgement” submenu.
Repair order status data includes e.g.:
• Scheduled / Rescheduled Date
• Scrap Information: Scrapped Locally, Total Scrap, Scrap Reason
• Status, Comments and Workscope
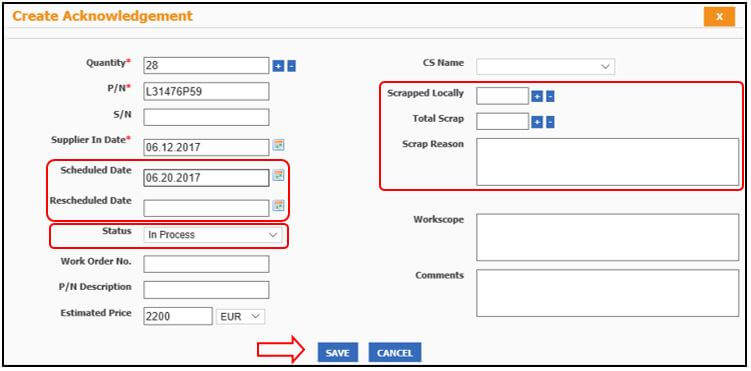
Click on “Save“ to secure the information entered and to close the submenu.
II.2.5 On Hold Start/Stop
You can initiate a “on hold” status and release it again for any specific repair order item. Please find the repair order you want to change status (see Chapter II.3.1. Repair Order Search) and open the repair order detail view (please see Chapter II.3.2. acknowledgment). Click on “On Hold” to get to the repair order “On Hold” screen.
Click on “START” to open the On Hold page.
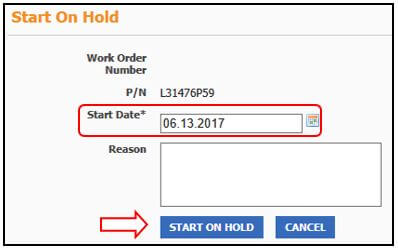
The On Hold start date is set to the current date but you can overwrite it if you are adding On Hold data for previous days. Please add an On Hold reason and click on “START ON HOLD” to send the On Hold information to your MRO customer. After closing the On Hold screen you will be back on previous screen. The On Hold information is now visible.

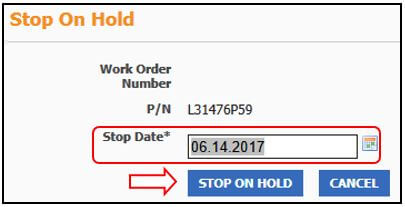
II.2.6 Return Shipment
In order to send the return shipment information for the serviceable and unserviceable parts please click on “Create Return Shipment” in the repair order detail view.
• Quantity shipped
• Supplier Out Date
• Material Condition
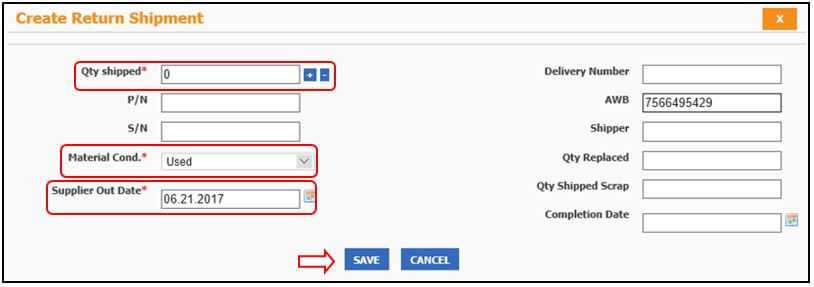
II.2.7 Upload Document
If your MRO customers requires documents from your company you can upload your file(s) directly into the MRO-Tracker. It will be connected to the repair order. Please go to “Repair Order Search”, type in the order number and click on “SEARCH”. Click on the repair order number to open the repair order details.
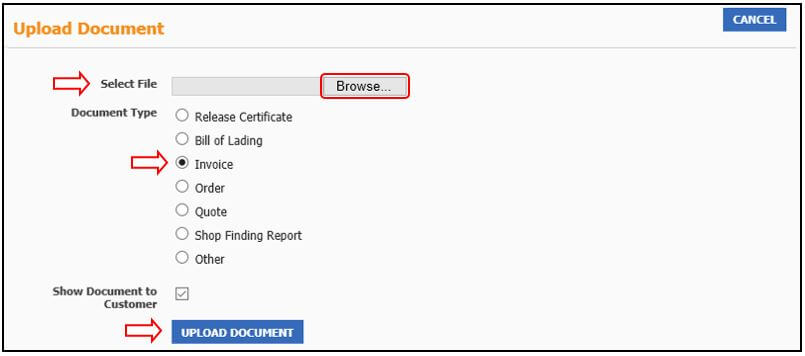

II.2.8 Messages
With the "Messages" feature, you have the option to send direct messages linked to the current repair order. This direct communication channel within the MRO-Tracker between you and your business partners saves time and helps quickly address critical issues related to a specific repair order item.To send a message, simply enter the first name, last name or email address of the supplier or customer contact you wish to reach, then add a subject, select a category and include the main message. You can also attach a file or include additional repair orders, as shown in the figure below.
Please confirm the transfer by clicking "SEND MESSAGE."
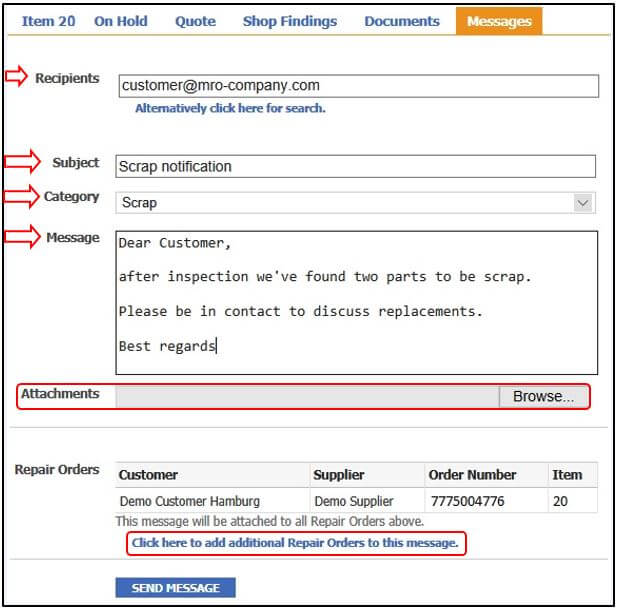
Additionally, a red notification will appear when the logged-in user is tagged/added as recipient in the message loop. The little blue envelop will wear a red dot indicating the number of unread user-tagged messages, ensuring users never miss an important update. This powerful feature inspires more efficient workflows, providing a seamless way to manage communication and track important information in one place.
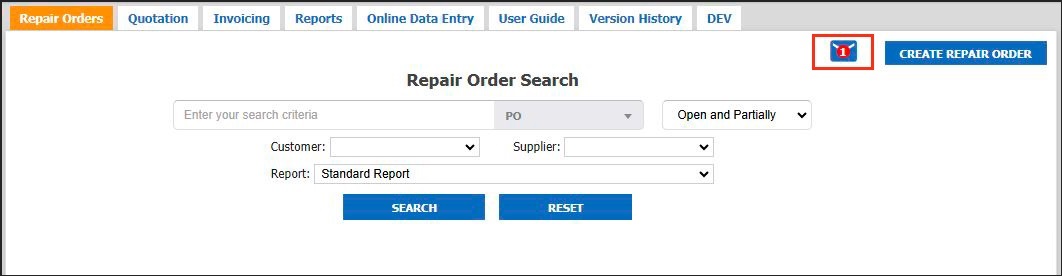
II.3 Reporting
II.3.1 Access a Report
II.3.1.1 Option 1: Using a shortcut or Advances Search Options
By clicking on a shortcut for “Standard Reports”, “My Reports” or “Shared Reports” on the repair order search page you will jump directly into the Reports section and find the query results according to the type of report you’ve selected. Alternatively use the Advanced Search Options to open a pre-filtered report.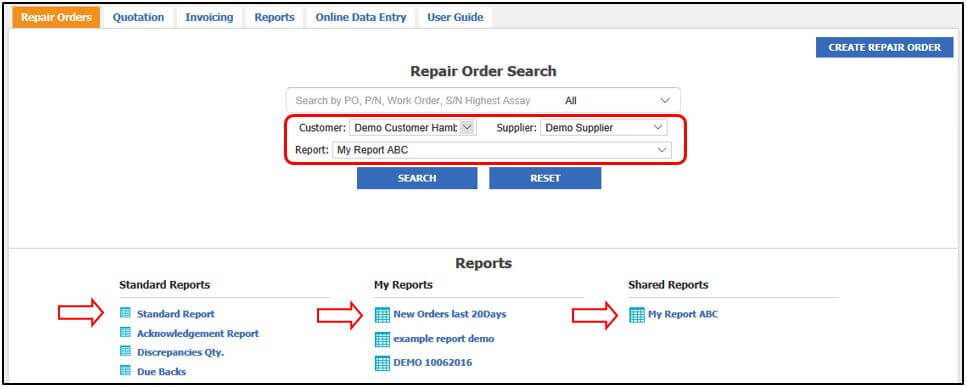
II.3.1.1 Option 2: Using the Reports panel
To access a specific report you can also navigate to the reports section and use the Reports panel. Move your mouse to the left side to expand the panel and choose from My Reports, Shared Reports, Standard Reports & Last Unsaved Reports.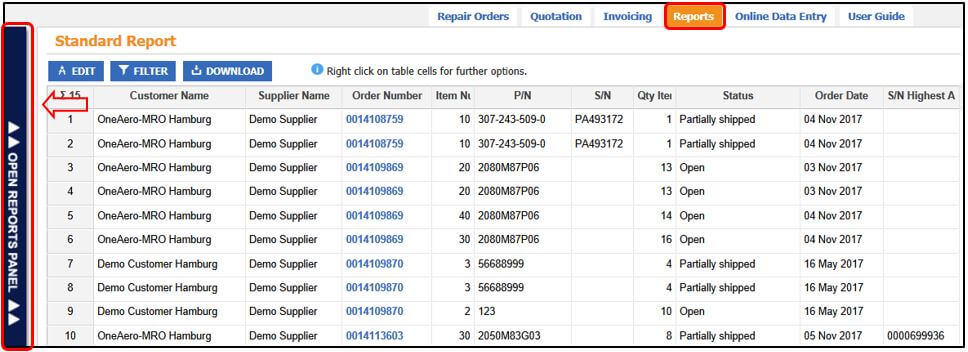
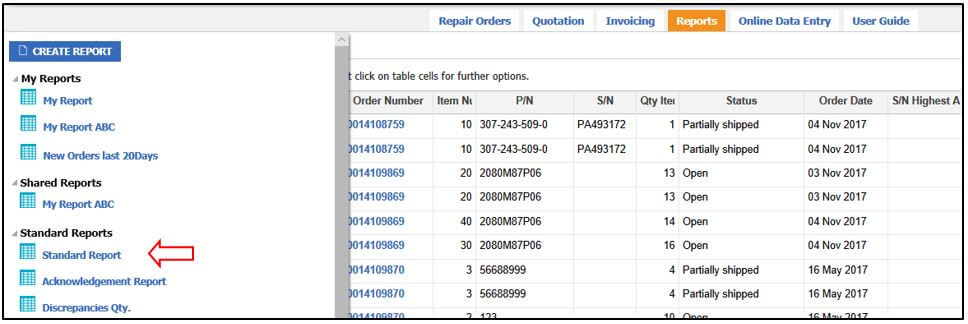
II.3.2 Filter a Report
If you want to further analyze the search results you can apply filter criteria to trim or individualize the report. Therefore you can either right click on a certain table cell to open the instant filter options:• filter this value
• filter excluding this value
• sort ascending
• sort descending
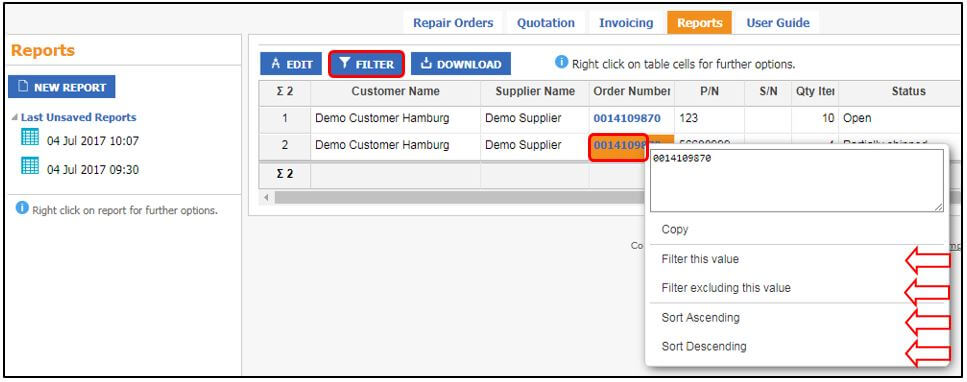
Or click on the “FILTER” button to extend the filter bar. Here you can select from different filter criteria which can be completed by using the data entry fields below (Example: Filter -> Customer Name -> “Starts with” & “Demo”).
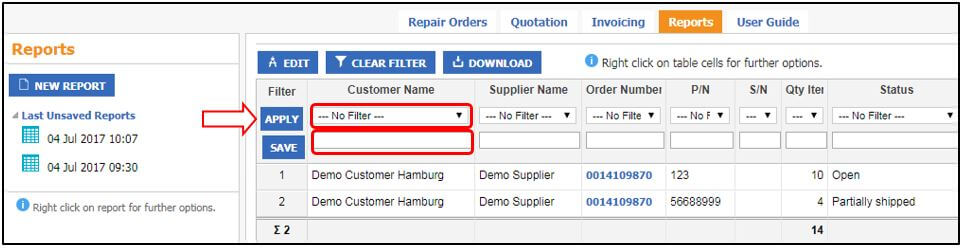
By clicking on “APPLY” – the current filters will be adopted immediately while using the “SAVE” button the filters will be added permanently to the report.
II.3.3 Create a New Report
Click on “NEW REPORT” in the “Reports panel” to get started. You can now choose between Tabular View (Excel format), Chart View (two axis diagram) and Pivot View (three axis diagram) to set the report format.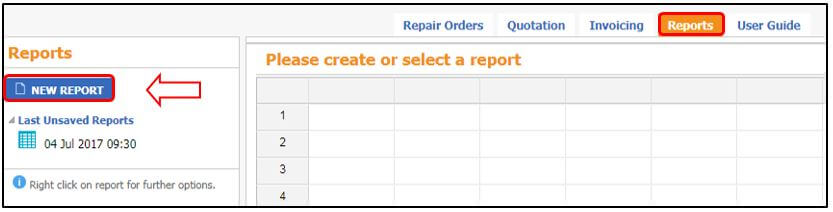
In the following section we will show an example for the Tabular view report.
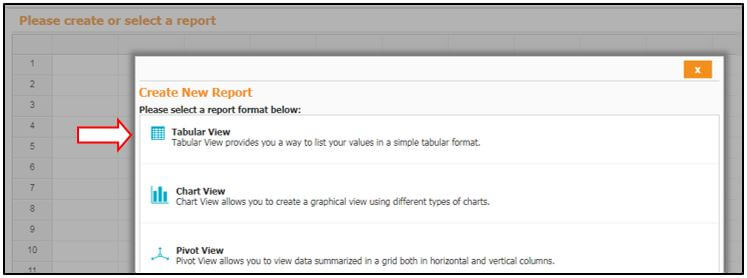
Click on “Tabular View” and continue to choose either an empty report or a predefined report (standard reports).
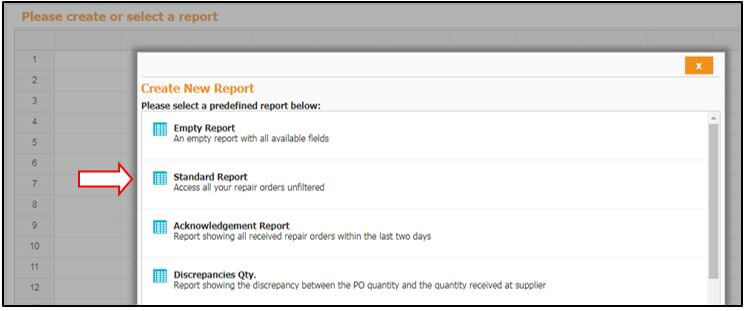
II.3.4 Run / Save / Download / Edit a Report
This is the structure of the report selected (Standard report). It shows the columns that are included and the filter already applied. You can now “RUN” or “SAVE” the report from here. Don’t worry if you forgotten to save a report – you can re-access unsaved reports through the reports panel. At the bottom you’ll find – Last Unsaved Reports. To secure the new report hit “SAVE” and give your report a unique name. Find your customized reports under “My Reports” on the repair order search page as well as in the reports panel.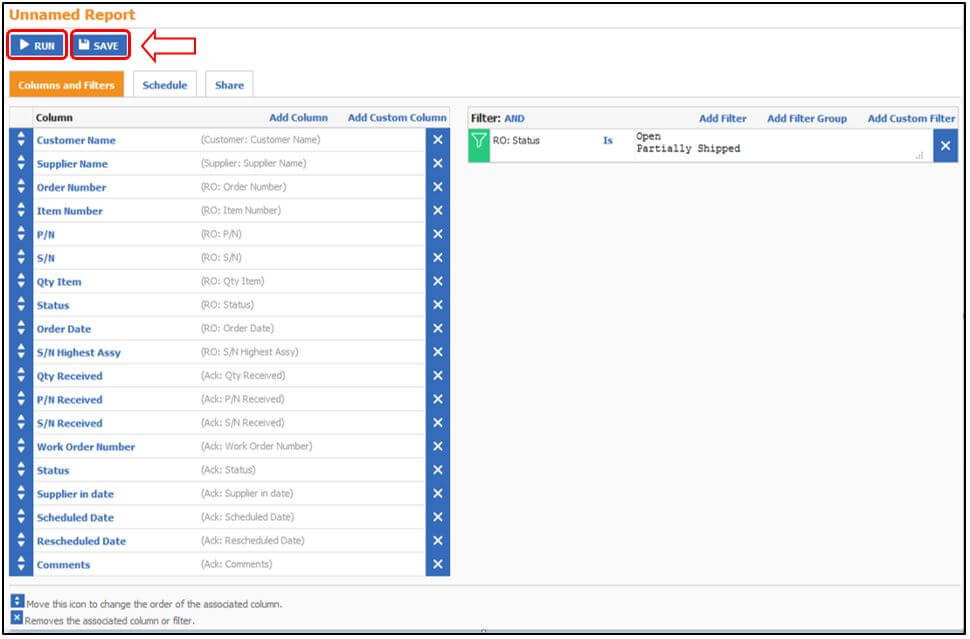
After you run the report you have several options to work with. You can “EDIT”, “FILTER” or “DOWNLOAD” the search results from your query. If you click on “FILTER” you have access to the functionality described in Chapter II.3.2 Filter a Report.

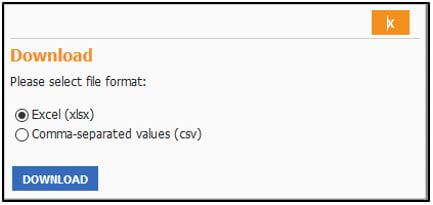
By clicking on “EDIT” you get back to the report structur page, where you have the ability to further customize your report. Here you can change the position of columns by Drag & Drop the left icon to your favourite order or remove them by using the [X] icon. To add columns click on “Add Column” and select a data field from different RO process categories. Also feel free to directly search for a certain data field by typing into the search box. After you clicked on “Add as Column” the corresponding data field will be added at the bottom of your report structure. Next to that you can add a custom column which for example could be a SUM/MAX/MIN/AVG of a certain data field. If you want to learn more about the option “Custom Column” and how to set up a calculated data field, please contact our support team. We’ll be glad to share further information and assist with the customization of your tailored report.
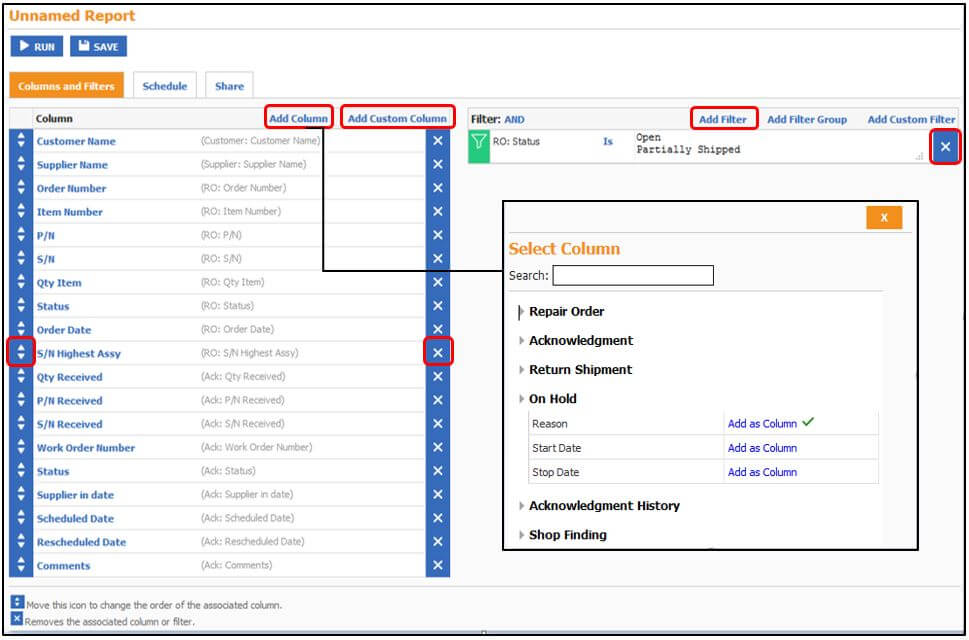
The same applies to the filter options. You can add and remove filters just as you do with columns. In simple filter consist of a data field (a), an operator (b) and a filter value (c). More complex filter will include nested queries between different data fields (see Overdue report template). By clicking on “Add filter” you open the same selection dialogue for data fields as depicted earlier. Please choose a data field and add an operator & filter value accordingly.
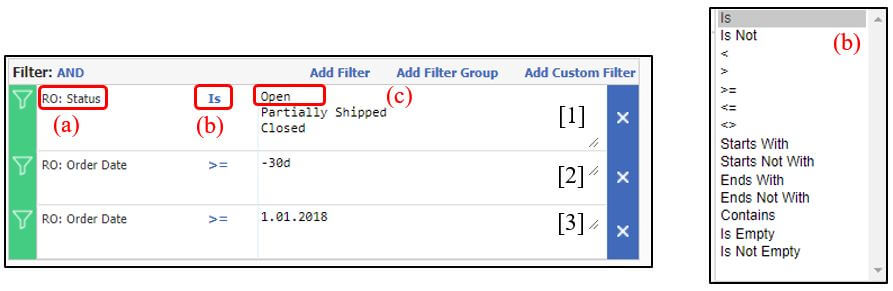
Please find some unrelated filter examples in the figure above [1-3]. You could just add different values separated by a line break in one filter. This is shown in example [1] where the filter will search for repair orders that have the status – Open or Partially Shipped or Closed. Another way to enter time filters is depicted in the filter examples [2 & 3]. In example [2] the filter is set to deliver repair orders whose order date is greater than minus 30 days from now or in other words: for the last 30 days (also use –m for month and –y for year). Example [3] will deliver all repair orders having an order date greater than the 1st January 2018.
If you encounter any problems or can’t get the report running, please don’t hesitate to be in touch with our support. We’d be happy to assist you on the instalment of your individual reports that reflects your needs.
II.3.5 Schedule a Report
After you successfully created a report you can schedule it for an automated e-mail delivery. Please note that you have to SAVE your report before you can schedule it! Run your preferred report than click on “EDIT” and navigate to “Schedule”. Here you can enter the criteria for your report distribution by e-mail (page scrolled up). Please confirm the checkbox “Activate Schedule” and enter a schedule interval, schedule time and contacts to be copied.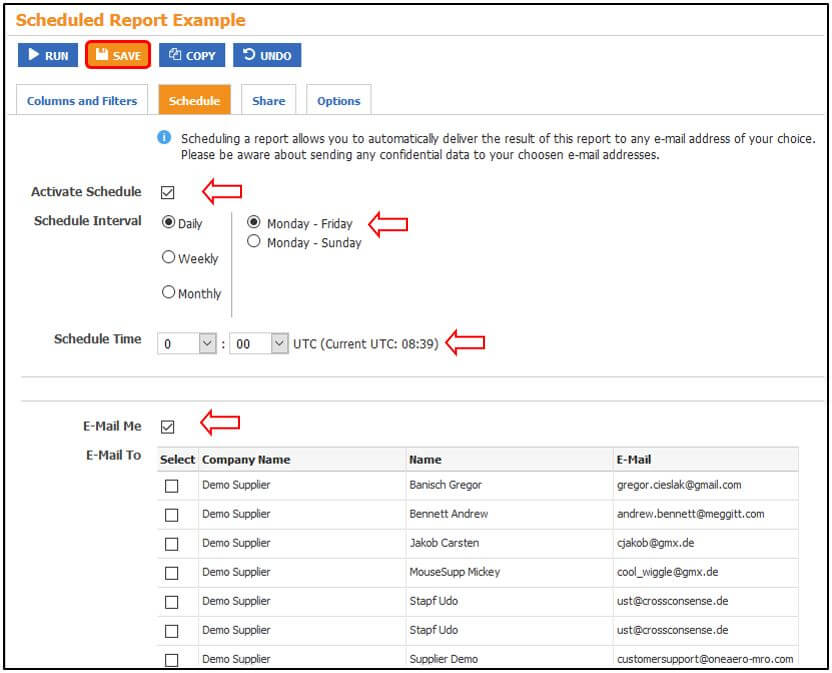
To automatically forward the report to an external contact enter his/her e-mail address in “E-Mail To” (page scrolled down). Also add an “E-Mail Subject” & “E-Mail Text” to inform about the content of the report. As a last option you can select the file format that will be attached. Please confirm your entries by clicking on “SAVE” at the top.
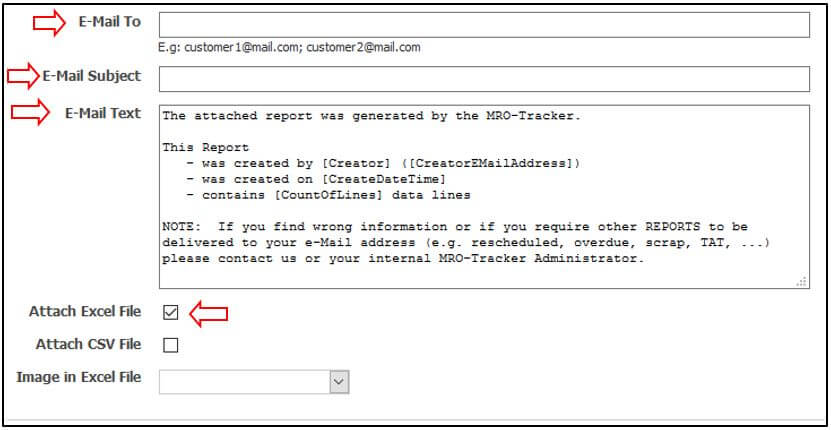
II.3.6 Share a Report
The MRO-Tracker allows to share a report once created. In this way your colleagues will be able to find the report in their own account and use it as a blue print or template to set up (their) reports. In order to share a report click on “EDIT” and navigate to “Share”. Here you have the option to set the permissions Allow Extentions and/or Allow Own Copy to the associated report. If you uncheck both boxes the shared report can only be seen and run from an other user. If you choose the option “Allow Extentions” every user can modify the report, which will affect all extended reports. In case you want to preserve the original report only click on “Allow Own Copy”. Consequently the shared report can be copied and modified, which will not take affect on the original report.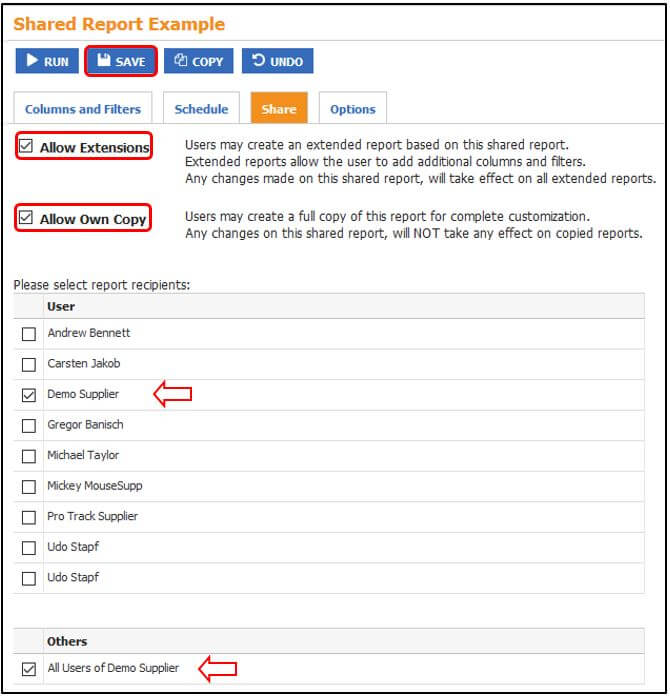
Please select the report recipients individually by clicking on the checkboxes next to the user name or share the report with all users of your company at the bottom. Finally confirm your entries by clicking on “SAVE”.
You can find shared reports on the repair order search page, the advanced search options and the reports panel (see Chapter II.1.1 and Chapter II.3.2).
II.3.7 Report Options
Accessing the “EDIT” functionality of a certain report you can change the report name & category under “Options”. By entering a different category name you will create a new category on the repair order search page, the advanced search options and inside the reports panel. This feature allows you to organize your reports and to clearly categorize them.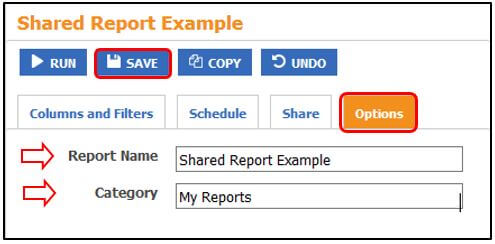
II.3.8 Report Context Menu
Whitin the expanded reports panel you have the ability to right-click on a certain report and open the context menu. This will grant you access to the functionality: “Run”, “Download”, “Edit”, “Rename”, “Set Category”, “Copy” and “Delete” right away. The “Set Category” button will allow you to rename the category and by this create a new category on the repair order search page as well as the advanced search options & within the reports panel.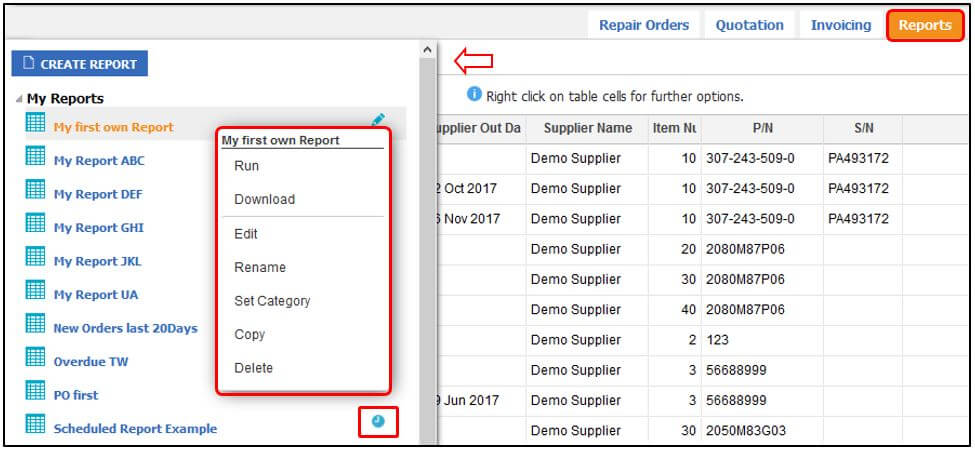
III Appendix - Support Contacts
b2b-aero.com GmbH
Schnellmark 30
23556 Luebeck
Mail: support@b2b-aero.com
Phone: +49-40-999 9999-0
IV Appendix – EDI implementation options & upgrade
Setting up the MRO-Tracker system („connection with ALL your business partners) is a ONE-TIME-EFFORT regardless of your IT knowledge, infrastructure or other EDI interfaces in place.With a one-time-implementation effort we can connect any ERP backend system with another and we are supporting data exchange projects between EDI or Non-EDI trading partners.
Below you find our implementation options available:
MESSAGE FORMATS:
• SPEC 2000/SITA
• XML
• XLSX
• CSV
• JSON
• OLE DB
•...
TRANSFER PROTOCOLS:
• HTTPS
• SMTP
• SFTP (FTPS)
• SOAP
• WEBSERVICES
• HTTP REST
• SITA
•...
INTEGRATION OPTIONS:
• online data entry (manual input)
• customized file transfer
• automated FULL EDI
Your preferred EDI option can be upgraded at any time in the future !
Please don‘t hesitate to contact the b2b-aero.com support team or key contact to discuss an upgrade in your existing EDI connection to our MRO-Tracker system. We‘ll be glad to help streamline your MRO EDI processes with the fitting EDI solution for your requirements.
IV Appendix - Capability listing
b2b-aero.com offers every vendor to take benefit of our capability listing tool – CAPABILITIES. Launched in July 2016 it provides an intuitive design and a fast self-taught upload process. The capability database includes accurate repair data such as part number, description, ATA Chapter, aircraft applicability and TAT. All companies that are using CAPABILITIES for sourcing purposes will now be able to search completely free of charge! This new policy aims at promoting our customers’ capabilities to a bigger prospect database, more than 35,000 aviation professionals from the b2b-aero.com network.
Are you interested in listing your capabilities on b2b-aero.com - Just send us an e-mail and we take care of the rest.
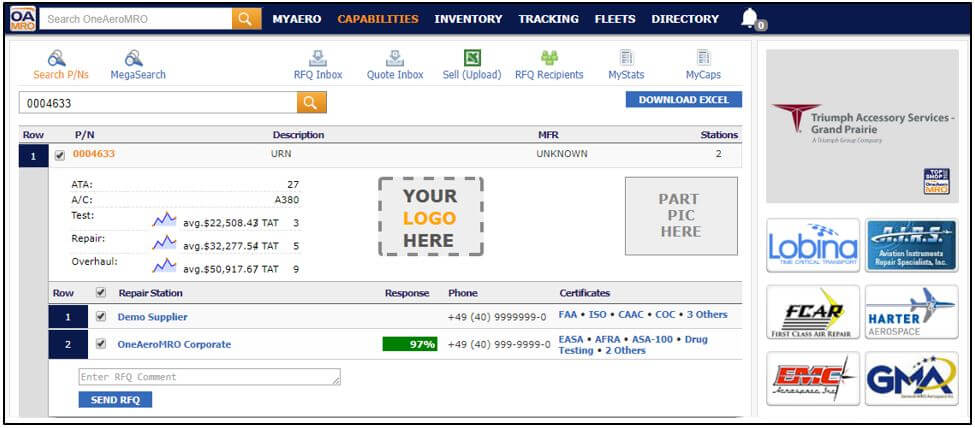